CASE STUDY
The Cosmetic Company improved working conditions with its new dust extraction system
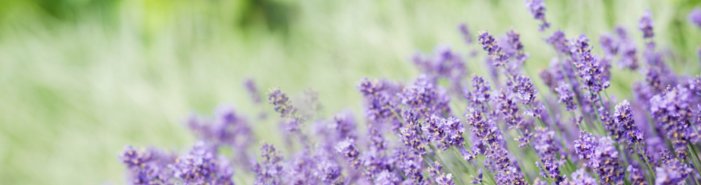
Working conditions in The Cosmetic Company’s blending room were very dusty and unpleasant. DUSTEX designed, manufactured and installed a dust extraction system that captured airborne dust at the source of its generation.
Background:
The Cosmetic Company’s blending facility comprises of a ribbon blender where bulk ingredients are measured and blended into talcum powder products. Once blended, a container filling machine is manually filled with blended product and weighed out into plastic containers for market distribution.
The problem:
The blending room can be very busy at times with up to three operators carrying out tasks such as opening bulk bags, blending ingredients, transferring product, filling containers, as well as other activities that contribute to the creation of dust clouds.
The blending room is isolated from the rest of the factory to prevent dust drift and contamination. However, the dusty conditions inside the blending room made working conditions unpleasant for the workers.
The Cosmetic Company wanted to ensure that their staff were not exposed to such dusty, unpleasant conditions and contacted DUSTEX to come up with a solution.
The solution:
A dust extraction system comprising of new hoods designed for the blender and the filling machine was installed. They were connected via galvanised ducting to a pulse jet dust collector with a fan that had been specially commissioned.
The hoods were designed to capture airborne dust at the source of its generation, before allowing it to escape into the workspace.
Since commissioning the new extraction system, conditions in the blending room have significantly improved and the operators are much happier in their work.
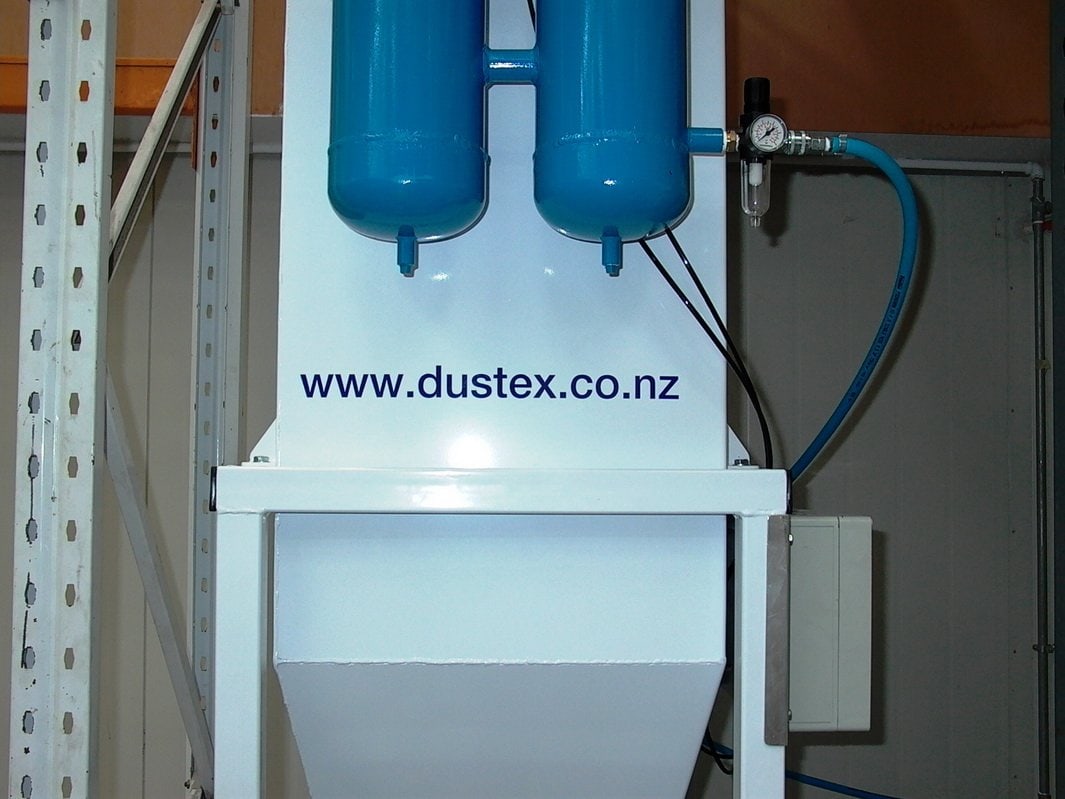